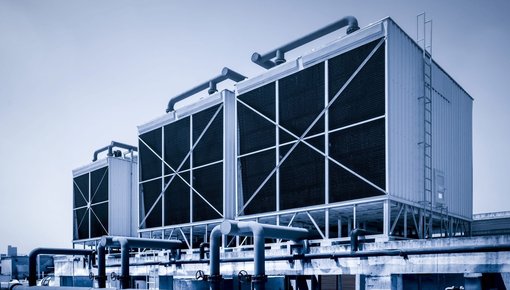
Cooling Towers
Goodway Benelux supplies cleaning agent for chemical cleaning of cooling towers from various manufacturers using the CIP (clean-in-place) procedure. It is also possible to clean the entire cooling circuit, including the connected chiller systems.
Read moreFouling in cooling towers
Both open and closed type cooling towers have to deal with fouling over time. Think of scale formation but also biological deposits. This fouling does not only stay in the cooling tower. In open cooling towers, the fouling can be transported with the flow of the water to the piping and connected heat exchangers such as the chiller or plate heat exchanger.
Chemical cleaning
Chemical cleaning using the CIP method (cleaning-in-place) is a relatively simple and effective way to clean cooling tower fill. A chemical cleaning agent, such as Scalebreak-MP, is added to the cold water basin. The mixture is then circulated with the natural flow of the cooling tower. As a result, the cleaning agent reacts with all parts of the cooling tower, but also the piping and connected heat exchangers, such as the chiller or plate heat exchanger. Ultimately, the cleaning agent ends up in the water distribution system. The nozzles distribute the cleaning agent over the fill, so that it can also be cleaned.
The biggest advantage of this cleaning method is that the connected piping and heat exchangers (in the case of an open cooling tower) are also immediately cleaned and descaled.
Cleaning-In-Place (CIP)
With a (preventive) CIP program it is possible to keep the cooling tower in optimal condition. Because the cleaning takes place preventively, the deposits cannot grow to an extreme level. This makes it possible to avoid early replacement of parts. Some other advantages of this method are:
- Saving manpower and labor, because the system can do the job itself. The cooling tower pump ensures that the cleaning agent ends up everywhere. It is therefore only necessary to add the cleaning agent to the cold water bassin and eventually neutralize and discharge it.
- Shorter downtime, because the installation does not have to be dismantled and the fill and other parts can remain in place during and after cleaning.
- Cost savings because parts do not have to be replaced early.
- During cleaning, it is possible to place air inlet louvers, drift separators and other components in the cold water basin. These will then also be cleaned.
- A preventive CIP program keeps the cooling tower and the entire cooling loop in optimum condition. Due to the high cleanliness of the installation, a stable, high efficiency close to the original values can be ensured. High cleanliness also contributes to a longer lifespan of the cooling tower and the associated heat exchangers, components, etc.