Power Generation Plants - Condenser Tube Cleaning
- Posted on
- By David Bokov
- 0
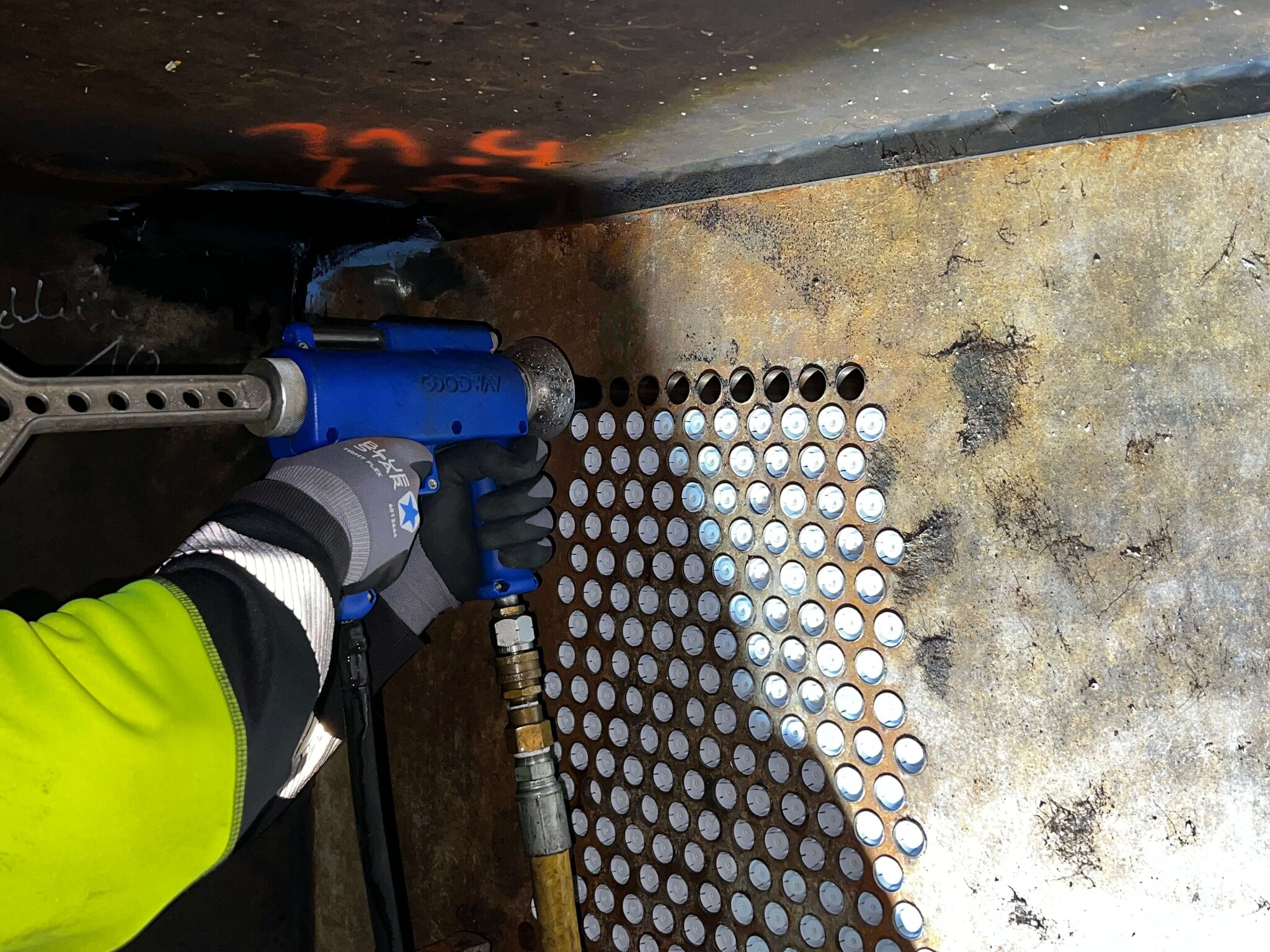
Steam surface condensers have a crucial role in the operation of power generation plants. Clean condenser tubes lead to increased efficiency of the system and therefore to a higher megawatt production. Goodway Benelux offers an innovative condenser tube cleaning solution for power plants in Europe. In short, a condenser with 10.000 tubes or more could be cleaned in a day or two. This blog explains the importance of a clean condenser, and shares insight into Goodway's condenser cleaning solutions. The blog also includes info, pictures and videos of a recent project in Denmark, where 15.600 condenser tubes had to be cleaned.
(Projectile) cleaning of condenser tubes
Steam surface condensers have thousands of tubes which have a cooling media (river-, sea-, or lake water) flowing through them. The condenser plays a crucial role in the power generating process. The cleaner the tubes, the better the heat transfer will be. The better the heat transfer, the higher the efficiency of the overal plant will be. Furthermore, it will lead to an increased production of megawatt output which means more revenue.
Some power plants have an online ball cleaning system installed on their condenser(s). Small balls flow through the tubes during operation of the condenser, which helps to keep the condenser tubes in decent state. In practice, though, a mechanical cleaning will still be required periodically. These cleaning balls do not choose the tubes that they go in; they are sucked into the tubes that have the highest flow. This means that some tubes will be cleaned more often and better than others. Also, these balls can get stuck in the tubes over time. This creates a blocked tube that has no flow. This ''deadzone'' in the tube can lead to corrosion and oxidation. In short, automatic ball cleaning systems might extend the cleaning interval time, they do certainly not exclude it. Surface condensers will always experience some sort of fouling, some more than others.
Projectile tube cleaning can be explained as follows: special projectiles are shot through condenser tubes at high-speed, with a low-pressure propulsion system. These projectiles remove deposits from the tube wall by scraping it off. One shot is usually enough to get a condenser tube clean. Projectiles are selected based on the (expected) fouling inside the tubes.
- Soft-medium deposits: Projectiles are the ideal match for deposits that are commonly found in condenser tubes of power plants. Some examples of these deposits are: sediment, silt, algae, slime (biofilm), sand, mud, sludge, zebra mussels and barnacles. Fouling like this can easily be removed with Goodway's nylon coil brush projectiles.
- Scale deposits: Some power plants have issues with scale deposits inside the condenser tubes. Depending on the hardness and amount of scale, Goodway's carbon steel projectiles could be a good solution. These types of projectiles remove the scale buildup through their high tensile carbon steel blades. In most cases a single pass will be enough to remove the scaling. In case of (serious) amounts of scale, a chemical cleaning would probably be the best solution, as it will leave a fully clean and smooth tube behind.
- Propulsion systems: The propulsion systems provide the power to actually shoot the projectiles through the tubes. This can be either an air powered system or kinetic hydrostatic pump, which uses 100% waterpower. Depending on factors such as fouling type, tube material, and previous experiences, one of both systems will be the best match.
Figure: Condenser tubes blocked with seawater deposits, like barnacles. Nylon coil brush projectiles removed all deposits in 1 shot. Cooling water can now flow through these tubes again.
Advantages of using a projectile tube cleaning technology
Projectile tube cleaning offers a number of advantages. In many cases, this technique is safer, faster, and more efficient and effective than traditional cleaning, such as high pressure lancing. Below you will find a brief summary of the main benefits:
- Speed: cleaning a surface condenser is usually perceived as a very time-consuming project. There's many tubes to clean, and the tubes are often many meters long. The time saved when cleaning with projectiles is substantial. The entire process of loading and shooting through projectiles takes less than 10 seconds per tube, regardless of the tube length. Up to 500 condenser tubes can be cleaned per hour, with 2 operators shooting through projectiles at the same time. This number can be increased by adding more operators. A surface condenser with 10.000 tubes can therefore be cleaned within 2 work shifts (say 8-10 hour shifts), or in other words, within 24 hours.
- Water consumption: the QS-300 uses compressed air and water in a 90/10 ratio. This means that only 10% water is used. The QS-300 uses approximately 18-20 liters of water per minute. Divided over a number of tubes, this results in a very low net water consumption per tube. Our kinetic-hydrostatic BFP pump system uses 132 litres/minute, but you only need about 10 seconds per tube. This amounts to approx. 20-25 liters of water per tube. This is a significant reduction compared to other cleaning techniques.
- Safety: the system uses a low pressure technology. This makes the cleaning process a lot safer for the operator. In addition, the tubes remain intact and undamaged, because they are not exposed to (extremely) high pressures. Projectiles are safe-to-use for titanium- and CuNi tubes. Just make sure the backside of the condenser is unmanned, but this is the same for any other cleaning technology.
- Costs: a projectile cleaning of a surface condenser usually ends up being much more affordable than other technologies (like high-pressure cleaning). Expenses will be won back quickly, by just a little increase in efficiency. A propulsion system is all that's required for a cleaning, which can be purchased or rented per project, and cleaning projectiles. As mentioned above, the type of projectile mainly depends on the fouling inside the tubes. The softer the deposits, the easier the cleaning process, and this leads to an overal lower project cost. Projectiles can be reused, as long as you make sure they have a soft landing on the backside of the condenser. For instance, take a seawater cooled condenser of a power plant, with 10.000 tubes, and soft-medium types of deposits like algae, mud, sludge, sediment, shells, mussels and/or barnacles. The power plant would be able to get its condenser cleaned with 2.500 pcs of nylon coil brushes, which would cost around €6.000,-. With 40.000 condenser tubes to clean, it takes 10.000 pcs of nylon coil brushes, which would cost around €25.000,-.
Project study: Biomass plant, 15.600 condenser tubes
In 2023, Goodway Benelux was contacted by a 360MW biomass power plant from Denmark. One of their seawater cooled condensers, consisting of 15.600 tubes, was significantly fouled. The condenser is equipped with an automatic, online ball cleaning system, but this wasn’t enough to keep the condenser tubes clean over time.
The condenser consists of 2 separate chambers, with 4 rows of 1950 tubes per chamber, making it a total of 15.600 tubes. Deposits such as biological fouling, sediment, mussels/barnacles, and a little layer of scale had to be removed, some tubes were completely blocked by the mussels. Nylon coil brush projectiles were used to clean the tubes, and shot through with Goodway’s kinetic-hydrostatic pump system (20-30 BAR, 130 l/min waterflow).
Figure: nylon coil brushes loaded in tubes.
To give an idea about the necessary equipment, the plant used a total of 4.000pcs nylon coil brush projectiles (= €10.000,-). These could be re-used 4 times, since they had a relatively soft landing on the backside of the condenser tubes.
Goodway Benelux supplied the cleaning equipment, and went over to Denmark for 2 days, to help during start-up. The operators on-site were trained to perform the cleaning themselves. Once they found their rhythm, the operators were able to clean 400-500 tubes per hour. The video hereunder illustrates the cleaning speed.
Preventive maintenance of the condenser tubes
Goodway Benelux's recommendation for power generation plants is a preventive cleaning and maintenance strategy for the condenser(s). When a mechanical cleaning occurs on a regular basis, deposits will remain soft in most cases, and therefore easy to remove with projectiles. Tubes do not get plugged with hard deposits and softer (nylon) projectiles can be used for the cleaning. This leads to a much easier cleaning process, less risk and lower costs. The costs for cleaning the condenser will be won back very quickly, by just a very minimal increase in efficiency. Ideally, condenser tubes are cleaned once per year, or worst case, once per 2 years.
When tubes are cleaned less often or not at all, the deposits will multiply further and grow into a harder substance. Fouling like limescale could occur, which is not easy to remove. At that point, it could be inevitable to use harder types of projectiles (such as carbon steel scrapers), high pressure cleaning (1000 BAR or more), or a chemical cleaning with a descaler. This could lead to much higher cleaning costs, more risk, and a much longer downtime of the condenser. Or in other words, a much more complex cleaning operation.
Additionally, fouling in condenser tubes not only negatively impacts the efficiency of the system, but it also poses a threat to the lifetime of the tubes themselves. When fouling is left unchecked for a while, the tubes can become corroded, ultimately leading to damage in the form of leakages. In the industry, this is often referred to as pitting corrosion. This type of damage is usually caused by, either or a joint combination, of under deposit corrosion (UDC) and microbiologically influenced corrosion (MIC). Usually, this form of damage goes unnoticed for a long time because the deposits cover it up - they keep the tube intact. As soon as the deposit (often scale) is removed, the damage will be uncovered. The customer might think that the cleaning technology has created damages inside the tubes, but it has merely uncovered what has been going on for a longer time. A preventive cleaning strategy ensures that deposits are removed as soon as possible, preventing them to grow and cause future problems.
In short, a preventive cleaning and maintenance strategy for power plant condensers pays itself back pretty easily. The condenser tubes remain clean, which increases heat transfer and thus the efficiency of the whole plant. Which down the line creates a higher megawatt production and thus more revenue for the company. Projectile tube cleaning offers a quick, but effective and safe solution to get clean condenser tubes.
Getting in contact
Are you interested to learn more about Goodway's projectile tube cleaning technology and equipment? Would you like to discuss if a projectile tube cleaning solution could be interesting for the condenser(s) of your (power) plant?
You can easily reach out to us, either by email, phone, or contact one of our people on LinkedIn. We can answer your questions, share more information, and if some more info is shared on your application, we can have a closer look and come up with a concrete advise how to maintain/clean it.
Click on this link to go to our customer service page and get in touch with us!
Comments
Be the first to comment...