Chemical Cleaning of Plate Heat Exchangers (CIP)
- Posted on
- By David Bokov
- 0
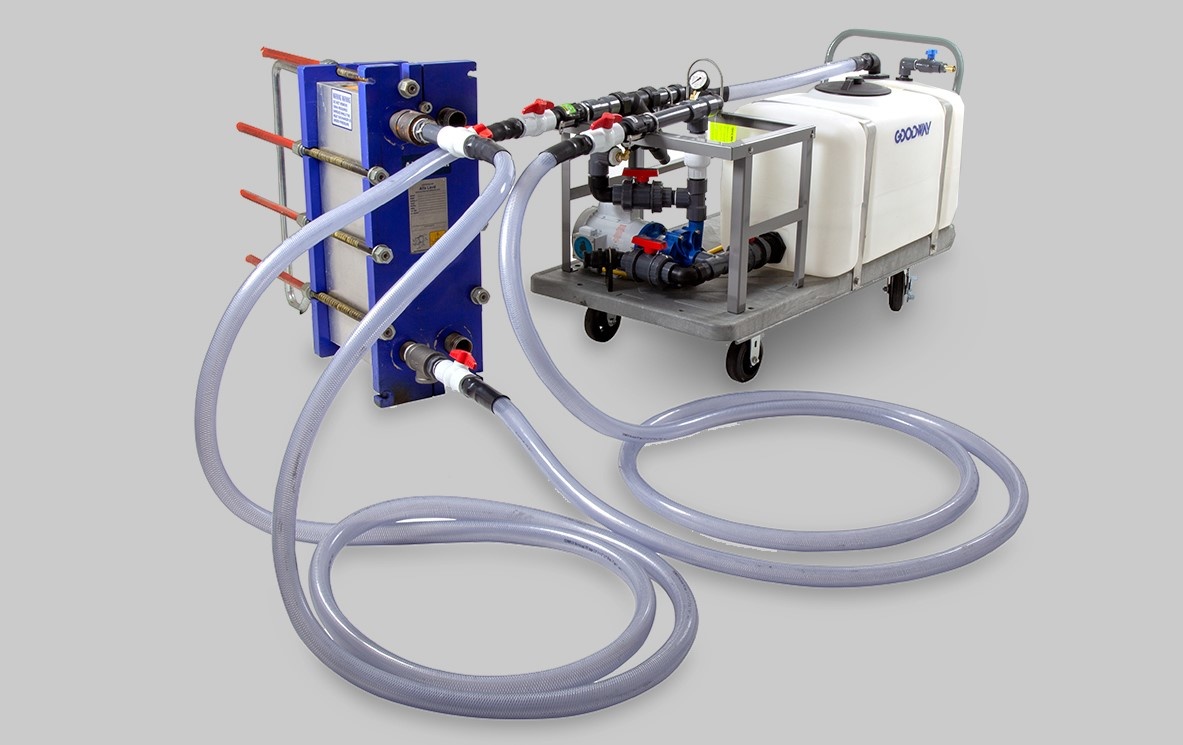
Commercial (HVAC) and industrial plate heat exchangers have to be cleaned periodically in order to operate at maximum efficiency. Thus also increasing the lifespan of the system. A chemical CIP could potentially offer a safer, easier and more effective cleaning process.
Cleaning of Plate Heat Exchangers
Commercial (HVAC) and industrial plate heat exchangers require a thorough, periodic cleaning in order to stay operating at peak performance. Furthermore, a clean system will have a longer lifespan than a (continuously) fouled system. In this blog we will talk more about the cleaning and maintenance of these type of systems.
In general, plate heat exchangers will suffer from fouling during their operation. Deposits in the plates will vary depending on the type of fluid going through them as well as other factors. These deposits can be anything from organic fouling up to hard scale formation. Depending on the deposits, different ways of cleaning can be selected. Each cleaning technology has its own advantages and disadvantages. In this blog we will talk about one of the most interesting methods: CIP (cleaning-in-place).
Cleaning challanges
With most cleaning technologies it is necessary to partially or completely disassemble the plate heat exchanger. Especially when disassembling plates, this can take quite some time and cause further complications such as leakages due to plates being reassembled incorrectly after the cleaning procedure. Some of the challenges when choosing to remove plates and cleaning them manually are:
- Disassembling the system and taking apart all of the plates individually takes quite some time and requires manpower. The more plates the heat exchanger has, the more time consuming this process will become.
- Gaskets can be damaged during disassembly and will also have a reduced lifespan due to the (de)compression. Did you know that the lifetime of gaskets is reduced by 50% when the heat exchanger is opened?
- Plates can be damaged during cleaning with high pressure, this can cause tiny leaks which can be hardly seen with the naked eye.
- If the system has to be cleaned off site, this will greatly increase the overall downtime.
By combining the above points, their associated costs and the total downtime, it is understandable that some companies try to postpone the cleaning as much as possible. Postponing the cleaning ensures that the deposit is able to increase over time. This can lead to a degree of deposits that is so high that mechanical cleaning is the only option. The longer the cleaning is postponed, the worse the efficiency of the installation will become, with all its detrimental consequences. Think of: increased energy consumption at less efficiency, malfunctions of the system and the like.
Cleaning-In-Place (CIP)
In most cases, a preventive CIP cleaning and maintenance program can offer a great solution. CIP basically means that the plate heat exchangers require as little disassembly as possible, before the cleaning can start. The system can remain on site and the plate pack can also stay compressed.
A flushing pump is connected by means of 2 hoses (bottom and top). After testing the circulation, a chemical cleaner can be inserted into the closed loop cleaning process. As the product comes in contact with the deposits, they are dissolved into a liquid suspension. Upon completion of the cleaning the used solution is freely flushed from the system along with the dissolved deposits leaving no residual solution. The main advantages of a CIP can be found below.
- By excluding the need for disassembly, the total cleaning time is reduced by a significant amount. In some cases customers have went from a downtime of 2-3 days to a total cleaning time of 8-12 hours.
- Less manpower is required due to the fact that the plate heat exchanger remains in place and does not need any transportation to an off site cleaning location.
- There is less risk of leaks after the cleaning, because the plates remain in place.
- Gaskets do not suffer from (de)compression and therefore do not have to be replaced.
- When a plate heat exchanger is running on a preventive maintenance program, the systems efficiency and lifespan greatly increase.
- All the above points lead to a significant decrease of cleaning and maintenance costs.
Goodway and SWEP have recently made a joint effort to assist customers with correct and preventive cleaning and maintenance equipment for brazed plate heat exchangers. Read more here regarding the joint effort between manufacturer SWEP and Goodway.
Applications
Plate heat exchangers can be found in virtually any industry. Ranging from small HVAC applications to central cooling systems of large container vessels. Regardless of the industry, all these heat exchangers need to be periodically cleaned in order to ensure an optimal heat transfer. In some industries, the cleaning frequency can be higher than others. Again, this completely depends on various factors.
A preventive CIP program is recommended in all cases. When the system is cleaned on a preventive base, the deposits will never grow to a point where the system has to be taken apart. Furthermore, this will ensure that the plate heat exchanger will always run near peak performance. Therefore, a preventive cleaning and maintenance program is often much more profitable than a reactive cleaning strategy.
Types of fouling
As chemical is flushed through the plates, it will dissolve deposits over time. In most cases a CIP is used to remove scale formation on plates, since scale increases the pressure drop and insulates the heat transfer surface, thus preventing efficient heat transfer. A little amount of scale formation can already have a detrimental effect on efficiency of the plate heat exchanger. In general, a chemical cleaner, such as Scalebreak-MP will dissolve the following deposits:
- Calcium
- Lime
- Rust
- Mussel shells
- Barnacles
- Mud
- Biological build-up
Optimal results are achieved when you pump into the bottom of the equipment and out the top. This method insures the area to be cleaned was flooded, allowing ScaleBreak-MP to come in contact with all the deposits. Adapting ScaleBreak-MP to your preventative maintenance program will insure peak efficiency, reduced operating costs and prolong the equipment’s useful life.
Comments
Be the first to comment...