Semi-automatic, low pressure tube cleaning
- Posted on
- By David Bokov
- 0
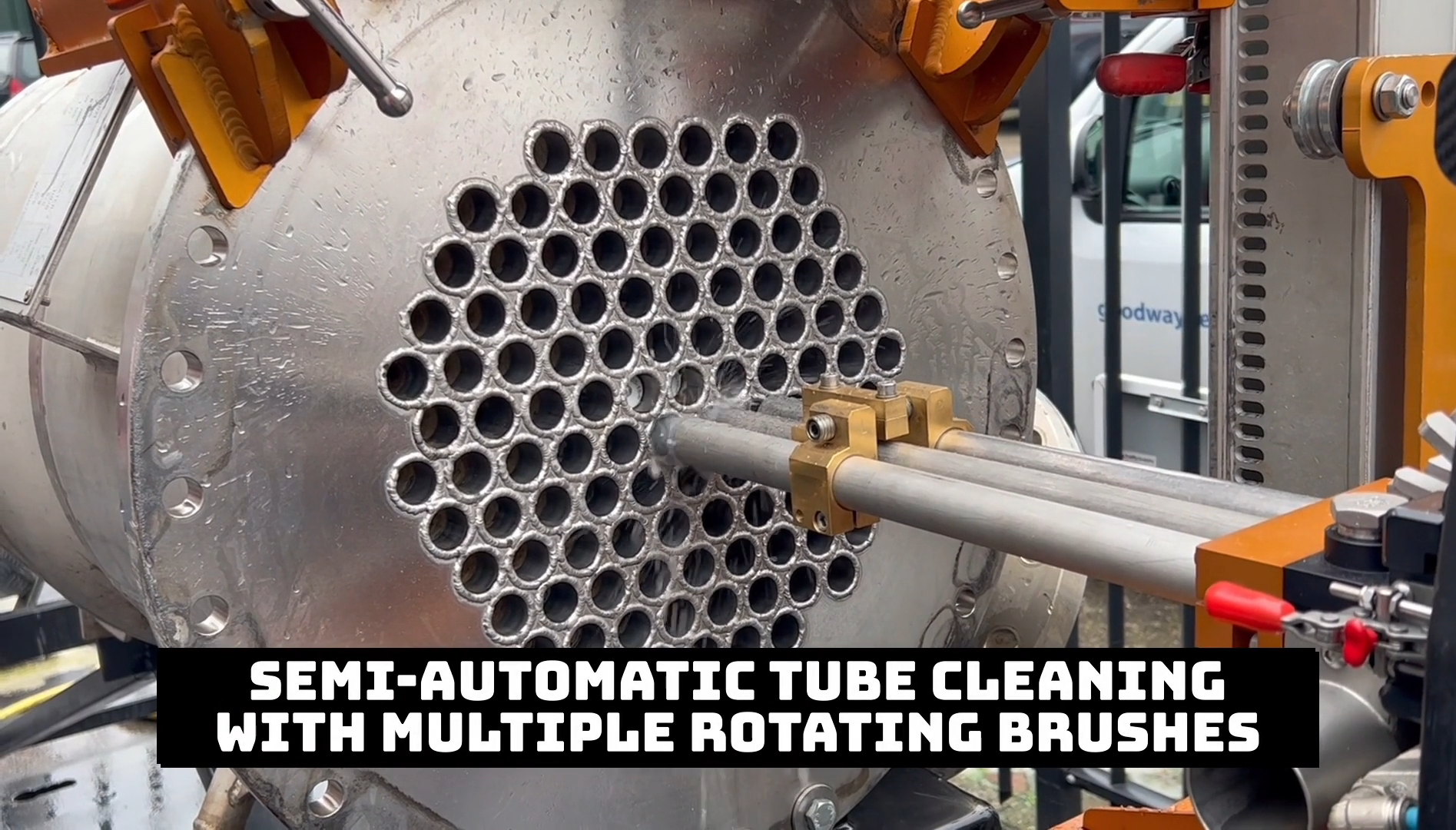
Recently Goodway Benelux and Peinemann Equipment have introduced their new innovation for semi-automatic cleaning and maintenance of heat exchanger tubes with high speed rotating brushes.
A new innovation for industrial tube cleaning
After a period of research, development and many tests, which took around a year to complete, the new innovation is finally ready for (industrial) usage. In this blog we will talk more in depth about the technology, it's benefits, areas of application and much more.
Industrial challenge
Lance feeding systems are used to push one or more high pressure lances/hoses through tubes at the same time, allowing for quick tube cleaning. The Goodway rotary tube cleaning systems are used manually, which means that an operator can only push 1 flexible shaft through the tube at a time. When you want to use 2 or 3 tube cleaners, it also means that 2 or 3 operators are required. This is not always possible due to: lack of space, manpower and more. Therefore, it is usually not interesting to use a rotary tube cleaning system for large(r) heat exchangers.
For these large(r) heat exchangers, Goodway rotary tube cleaning systems are mostly used for a 2-pass cleaning before inspections have to take place, think of: IRIS or eddy current testing of tubes. The oversized brushes often remove a last remaining layer of deposits, even after a high pressure cleaning. The brushes not only clean but also polish the tubes, raising the cleanliness level of the tubes even higher. Furthermore, if the deposits have a soft to medium characteristic, the rotary tube cleaning equipment can also be used entirely instead of high pressure. Usually this is done for smaller heat exchangers, chillers, evaporators and more. (500-1000 tubes max.)
The innovation
After an extensive collaboration between Goodway Benelux and Peinemann Equipment, we have developed a new innovation: semi-automatic, low pressure tube cleaning. This technology combines the best of both worlds:
- Goodway rotary tube cleaning systems, like the ''air powered AWT-100X''.
- The Peinemann feeding system ''Triple Lance Tube Cleaner (TLX)''.
The combination of Goodway- and Peinemann equipment makes it possible to clean tubes at high speed with low pressure, all semi-automatically. It is therefore possible for the operator to clean several tubes at the same time without having to manually push the shaft through the tubes. When set-up, 1 operator can control the entire cleaning by him/herself, even if this is a setup with 3 Goodway tube cleaning systems. This ''upgrade'' delivers a significant increase in cleaning speed and significantly reduces the labor of the operator(s). This innovation therefore allows end customers and contractors to choose from more cleaning technologies when cleaning large(er) heat exchangers.
Why low pressure?
In the world of industrial cleaning, a contractor is usually inclined to use high pressure equipment to clean the inside of heat exchanger tubes. This can vary from 200 up to 2500+ bar. This method of cleaning is perfect for (very) hard deposits and blocked tubes. Industrial heat exchangers can often become very polluted, a high pressure cleaning offers the solution.
However, this is not always the right solution for heat exchangers with soft to medium deposits. For these type of deposits, a low-pressure cleaning technique is a better solution. Cleaning tubes with rotating brushes is a simple, yet effective technology. The rotating brush removes deposits from the tube walls by rotating at a high speed, while a light water flush ensures that the deposits are removed from the tubes. Below are some features/advantages of the method:
- During a low-pressure cleaning, a brush rotates at high speed through the tubes, this is the only part that actually performs the cleaning. The water flush (2-3 bar) ensures that the loosened deposits are actually removed from the tubes. The risk of, for example, damage and/or injury is thus minimized. This also means that the SIR guidelines do not apply to this cleaning method.
- Because less water is used during cleaning (10-15 liters/minute per system), the amount of waste water is minimized. (At least 80%)
- The most commonly used brushes are made of nylon material, which means that the bristles cannot damage the tubes. This makes it possible to clean fragile tubes made of softer metals. Think of: copper/nickel and titanium tube materials as an example.
- For soft to medium deposits (sludge, algae, mud, etc.) it is possible to use this technology as the main cleaning method. In that case, it is no longer necessary to carry out a high-pressure cleaning beforehand. This significantly decreases costs of cleaning and downtime of the installation.
- Use this technology as a 2nd pass after a high-pressure cleaning prior to tube inspections (IRIS, eddy current etc.) After a high-pressure cleaning, a small layer of deposits may still remain inside the tubes. The oversized, rotating brushes will remove that last remaining layer of deposits.
Video: low pressure tube cleaning
Areas of application
This combined equipment can be used for a large variaty of industrial cleaning applications. This type of equipment is mostly used for installations at industrial sites such as refineries or production plants. The high speed rotating brushes are effective against soft to medium deposits. Some examples include:
- Shell & tube heat exchangers
- (Watercooled) chillers and condensers
- Fin/fan cooler tubes (inner cleaning)
- Tubular evaporators
The blue flexible shafts of Goodway require a constant amount of low pressure cold water. This water will be pushed through the shafts and eventually flush out loosened deposits during the cleaning process. The water also acts as a cooling medium for the rotating core of the shaft which is made out of high resistance galvanized steel.
The Peinemann system is versatile and can be used for many, different applications. Click on this link for more information.
Peinemann lance feeding systems
The Peinemann TLX has a push/pull strength of approximately 120 KG. This force is required to push and pull the 3 flexible shafts and oversized brushes through the tubes, simultaneously. During cleaning, the brushes create a high amount of friction and resistance. Therefore a 120 KG push/pull strength is absolutely necessary for this combination to function successfully.
Using multiple rotating brushes at the same time is different from using high pressure hoses. The forces acting on the bundle cleaner and the frame are a lot stronger. The various tests that have been carried out have shown that the Peinemann setup including the TLX system is the right one.
Furthermore, a number of specific modifications must be made to both the Goodway- and Peinemann systems. After all the tests, Peinemann designed and applied the right modifications, so that the combination of the equipment can be used safely and sustainably. Goodway Benelux and Peinemann Equipment both have the knowledge to advise and implement the correct modifications. It is also possible to modify already existing Peinemann systems.
Interested to learn more?
If you are interested to learn more about this innovation, please feel free to reach out to us. Our experts are more than happy to talk with you about this and other solutions.
Schedule a call with one of our experts here.
Comments
Be the first to comment...