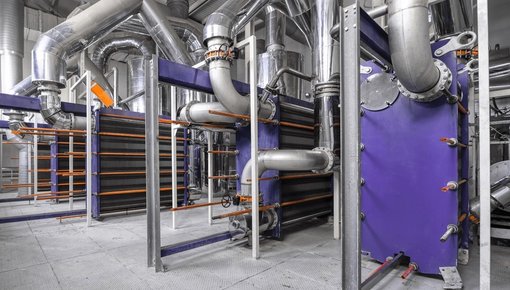
Plate Heat Exchangers
Goodway Benelux supplies descaling pumps and cleaning agent for the chemical cleaning and descaling of plate heat exchangers. Remove scale and biological deposits using the CIP (clean-in-place) procedure.
Read moreCleaning and descaling plate heat exchangers
Goodway Benelux supplies descaling pump systems and industrial descaler agent for the cleaning and descaling of plate heat exchangers. Plate heat exchangers have a crucial role in various operational processes. It is therefore extremely important to keep these systems in good condition. A fouled plate heat exchanger will be less efficient and still consume the same level (or even more) energy. In addition, the lifespan of the installation and components can be shortened by keeping it in a fouled condition. The (preventive) cleaning and descaling of plate heat exchangers is therefore very important.
How to clean plate heat exchangers
In many cases it is possible to clean and descale plate heat exchangers using the CIP (clean-in-place) procedure. In this technique, a descaling pump system is used to circulate a cleaning agent (descaler) through the plates of the heat exchanger. A CIP is a very simple and effective technique for cleaning plate heat exchangers, especially with a preventive cleaning and maintenance program in place. On this page you can find more detailed information about how a CIP works.
With a CIP program, more plate cooler cleanings will take place on an annual basis than with a mechanical cleaning. However, despite the higher frequency of cleaning, this technique is a lot more affordable for the customer and better for the system. This is due to the following factors:
- Less manpower required, because the system does not have to be disassembled.
- Shorter downtime, because the system does not have to be disassembled. In some cases, the total downtime due to cleaning can be up to 80-90% shorter. Of course, this also has a direct link with cost savings.
- Cost savings because gaskets do not have to be replaced. The lifetime of the gaskets is reduced by 50% when the plate heat exchanger is disassembled. This is due to the compression and decompression of the plates.
- A preventive CIP program keeps the plate heat exchanger in optimum condition. Due to the high cleanliness of the system, it is possible to ensure a stable, high efficiency close to the original values. High cleanliness also contributes to a longer lifetime of the system and the internal components, such as the gaskets.
A good combination of the cleaning agent (descaler), the mix ratio and the type of descaling pump system will ultimately determine the cleaning result of the CIP. That is why you should always consult an expert before carrying out a cleaning-in-place.
Importance of cleaning and descaling plate coolers
The efficiency of a plate heat exchanger / plate cooler is determined by the efficiency of the heat transfer. When there is fouling, the efficiency can drop quickly. This is because deposits have an insulating effect. The (preventive) cleaning and descaling of the heat exchanger is therefore extremely important. Cleaning and descaling can be carried out quickly and easily using the CIP method, as described above. When cleaning and descaling are carried out preventively, this will contribute to a stable efficiency of the heat exchanger as well as a longer lifespan.
Scalebreak-MP descaler
Scalebreak-MP (multi-purpose) is the most widely used descaler of Goodway Benelux. This is because it is hazardous-free, biodegradable and can be used on almost any material. In addition, gaskets remain unaffected during cleaning with Scalebreak-MP, so little or no new parts are needed. Some types of materials which are unharmed by Scalebreak-MP are:
- Brass
- Copper
- Nickel
- (Stainless) steel
- Rubber
Current cleaning techniques
At the moment many end customers and contractors still use the traditional cleaning method of cleaning plates manually with high pressure washers. In this case, the entire system has to be disassembled and the plates are cleaned piece by piece, sometimes also mechanically brushed. This is an intensive job and can easily take a few days. The costs for this cleaning technique are often high, due to the following factors:
- Disconnecting and disassembly of the system
- Transport of the plates to an offsite location for cleaning
- Manual cleaning of the plates, piece by piece
- Checking plates for hairline cracks caused by high pressure cleaning
- Replacing gaskets of the plates
- Reassembly of the system
By combining the above points, their associated costs and the total downtime, it is understandable that some companies try to postpone the cleaning as much as possible. Postponing the cleaning ensures that the deposit is able to increase over time. This can lead to a degree of deposits that is so high that mechanical cleaning is the only option. The longer the cleaning is postponed, the worse the efficiency of the installation will become, with all its detrimental consequences. Think of: increased energy consumption at less efficiency, malfunctions of the system and the like.